Opening the Power of Welding WPS: Approaches for Performance and Security in Fabrication
In the realm of fabrication, Welding Treatment Specs (WPS) stand as the foundation of welding operations, dictating the necessary steps for attaining both performance and safety in the fabrication procedure. Comprehending the intricacies of WPS is extremely important to using its full potential, yet many companies have a hard time to unlock truth power that exists within these files (welding WPS). By diving right into the strategies that optimize welding WPS, a world of boosted efficiency and increased safety awaits those willing to explore the subtleties of this important facet of manufacture

Importance of Welding WPS
The value of Welding Procedure Requirements (WPS) in the construction industry can not be overstated. WPS work as a crucial roadmap that describes the needed actions to ensure welds are performed regularly and properly. By specifying necessary parameters such as welding processes, materials, joint designs, preheat temperatures, interpass temperatures, filler metals, and post-weld warm therapy demands, WPS offer a standardized technique to welding that boosts performance, top quality, and safety and security in manufacture procedures.
Adherence to WPS assists in accomplishing uniformity in weld top quality, minimizing the chance of issues or architectural failings. This standardization additionally promotes conformity with market policies and codes, guaranteeing that fabricated structures fulfill the called for safety and security requirements. Additionally, WPS paperwork enables welders to replicate effective welding treatments, resulting in consistent outcomes across different projects.
Basically, the thorough development and stringent adherence to Welding Procedure Specifications are extremely important for supporting the stability of welded frameworks, safeguarding versus prospective risks, and promoting the reputation of manufacture business for delivering high-quality services and products.
Crucial Element of Welding WPS

Enhancing Effectiveness With WPS
When optimizing welding procedures, leveraging the crucial aspects detailed in Welding Treatment Requirements (WPS) comes to be necessary for improving processes and maximizing productivity. One means to improve performance with WPS is by very carefully picking the proper welding specifications.
Moreover, appropriate training and accreditation of welders in understanding and implementing WPS can even more boost efficiency. Ensuring that all team participants are fluent in interpreting and implementing the WPS precisely can reduce mistakes and remodel, saving both time and resources. that site Routinely evaluating and upgrading the WPS to integrate any lessons found out or technical improvements can also add to effectiveness enhancements straight from the source in welding operations. By welcoming the guidelines stated in the WPS and continuously seeking methods to enhance procedures, producers can accomplish higher performance levels and exceptional end outcomes.
Ensuring Safety in Fabrication

Safety and security methods in construction play a crucial duty in safeguarding personnel and optimizing functional procedures. Guaranteeing safety and security in manufacture entails a complex technique that includes numerous aspects of the welding process. One essential element is the stipulation of individual protective devices (PPE) customized to the details threats existing in the construction atmosphere. Welders must be furnished with appropriate equipment such as helmets, handwear covers, and protective clothes to mitigate threats connected with welding tasks.
Furthermore, adherence to proper air flow and fume removal systems is critical in maintaining a healthy workplace. Welding fumes include hazardous substances that, if breathed in, can posture significant wellness risks. Executing efficient air flow actions assists to minimize exposure to these hazardous fumes, promoting respiratory health and wellness amongst workers.
Normal equipment maintenance and examinations are also vital for making certain security in manufacture. Defective equipment can lead to mishaps and injuries, highlighting the relevance of regular checks and timely repair services. By prioritizing security actions and cultivating a society of understanding, fabrication centers can create a safe and secure and productive workplace for their workers.
Executing WPS Best Practices
To improve functional effectiveness and make certain quality outcomes in construction procedures, integrating Welding Procedure Requirements (WPS) best techniques is critical - welding WPS. Executing WPS finest methods involves meticulous preparation, adherence to market criteria, and continual monitoring to guarantee ideal results. Firstly, selecting the proper welding procedure, filler material, and preheat temperature level specified in the WPS is important for attaining the wanted weld high quality. Secondly, guaranteeing that certified welders with the needed accreditations execute the welding treatments according to the WPS guidelines is vital for consistency and reliability. Routinely updating and reviewing WPS records to show any procedure enhancements or modifications in materials is also a vital finest practice to keep accuracy and relevance. In addition, supplying extensive training to welding employees on WPS demands and best techniques promotes a culture of safety and security and high quality within the manufacture atmosphere. By diligently applying WPS ideal methods, fabricators can enhance their operations, lessen errors, and provide superior items to meet client assumptions.
Conclusion
In conclusion, welding WPS plays a critical function in ensuring efficiency and safety and security in fabrication procedures. By following these methods, companies can open the full potential of welding WPS in their construction operations.
In the realm of fabrication, Welding Procedure Specs (WPS) stand as the backbone of welding procedures, determining the required actions for attaining both effectiveness and safety in the manufacture procedure. review By specifying essential parameters such as welding processes, products, joint designs, preheat temperatures, interpass temperature levels, filler metals, and post-weld warm therapy demands, WPS provide a standardized technique to welding that enhances effectiveness, high quality, and security in manufacture processes.
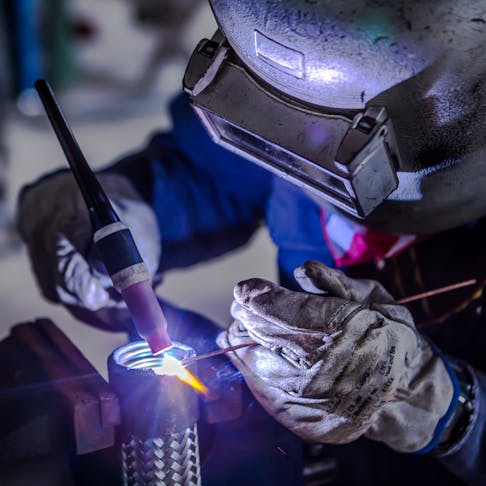
When maximizing welding operations, leveraging the vital elements detailed in Welding Treatment Requirements (WPS) becomes crucial for simplifying processes and optimizing performance. (welding WPS)